Let’s be honest—your supply chain could probably use a little freshening up. Over time, waste piles up. Processes get messy. Costs creep higher. That’s why now is the perfect time to clean up your logistics operations. When you focus on trimming the fat, everyone benefits—especially your bottom line.
Start with Least Cost Provider Reporting
TLI’s Least Cost Provider (LCP) reporting gives you a powerful tool to find transportation savings. You can track every shipment and see which carrier delivered at the lowest cost. This helps you avoid overpaying for similar routes or services. Similarly, it lets you track unrealized savings by exhibiting what you could have saved had you or your vendor actually used the LCP motor carrier on a historical basis. We can use this data to run supply chain planning scenarios based off various motor carrier models.
ViewPoint TMS makes this even easier when you have a live shipment to book. It automatically selects the most economical carrier every time. No guesswork. No spreadsheets. Just smart, cost-effective choices. If you’re not using it, you’re likely overspending.
Vendors matter too. ViewPoint TMS offers an Inbound Vendor Portal. This tool lets key vendors log in, tender shipments to you, and remain accountable during carrier selection. You can even enforce LCP usage so your partners ship smarter—not just faster. Finally, it also can aid you in forcing vendors to consolidate freight which not only reduces freight costs, it trims back environmental emissions. So you can ironically save green, by going green.
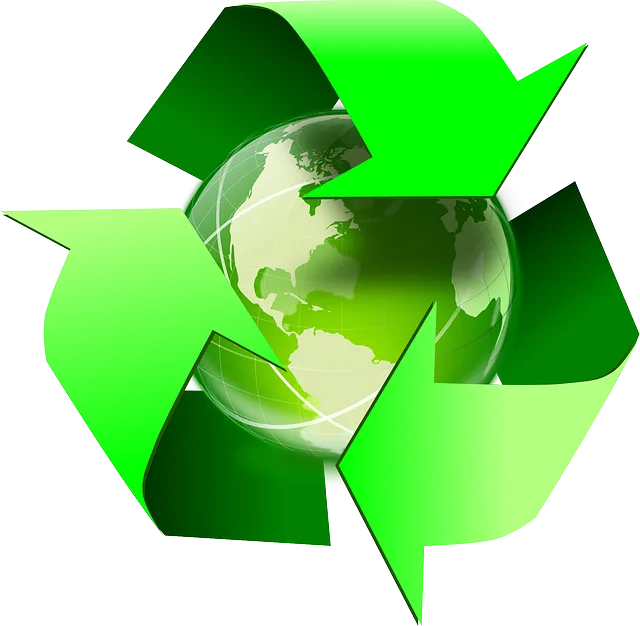
Recycle, Repurpose, and Reduce Waste
Packaging waste adds up quickly. But many smart shippers reuse dunnage and packaging materials from inbound shipments. This cuts costs and waste at the same time. A little creativity here goes a long way.
Get your teams aligned. Encourage warehouses to separate, repurpose, and reuse materials. This doesn’t just save money—it shows environmental responsibility too. Many vendors already use returnable packaging. Tap into that.
Also, consider revisiting packaging specs. Are you using the right size boxes? Are void-fill materials necessary? Small tweaks can lead to big savings in both cost and space and adding extra packaging can lower risks of freight claims.
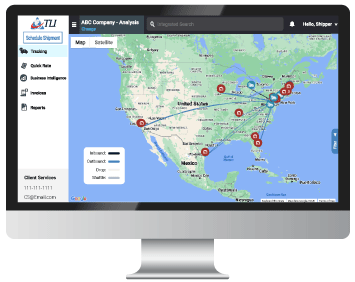
Use Your Data—Don’t Ignore It
Data drives smart decisions. If you’re not analyzing shipment trends or vendor performance, you’re flying blind. Use the dashboards powered by ViewPoint TMS to see what’s working and what’s not.
You don’t have dashboards? No problem. Consider connecting ViewPoint TMS to Power BI or your ERP system. That way, your team can visualize freight spend, carrier performance, and missed opportunities.
Once your data is live, dig deep. What routes cost the most? Are you using the most efficient carriers? Where do delays happen? Let the numbers show you the way forward.
Optimize Inventory Placement
A big part of logistics efficiency comes from inventory placement. Don’t store products based on guesswork. Use actual usage data and turnover rates. Items that move fast should sit close to shipping stations.
You’ll speed up pick times and reduce storage costs. If you’re shipping across the country often, consider opening a satellite warehouse. Fewer miles mean fewer dollars spent.
Spring is a great time to do an inventory audit. Clean up old stock. Move slower items to less valuable space. Focus prime locations on fast-moving goods. The most impressive layout of a warehouse I have seen was built specifically ahead of time to optimize the productivity of production with the placement of raw material and inventory.
The facility I am mentioning had a layout similar to a horseshoe. The docks have inbound on the left side and outbound on the right side. The inbound after being unloaded are promptly taken to the entire left side of the facility and the most-used raw material is placed closest to production. The production facility is located in the back right of the facility and as the production is completed the finished goods are then placed in the inventory section directly behind the right side of the docks – the outbound stations.
This customer advised that not only did this aid accountability, reduce bottlenecks, and improve speed & efficiency it also resulted in a safer facility.
Ensure Production Has What It Needs
Production delays kill efficiency. Missing parts slow everything down. The recent wave of tariffs and supply chain disruptions makes this even harder.
Work closely with purchasing to align deliveries with production needs. Build safety stock into your supply chain when it makes sense. This keeps lines moving—even when surprises hit. Have marketing provide your purchasing teams with forecasts so they can plan for projected demand in-advance.
Track vendor reliability. ViewPoint TMS can show you which suppliers deliver on time and which ones fall short. Use that data to plan smarter and hold partners accountable.
Three More Ways to Optimize Logistics Operations
1. Streamline Transportation Planning:
Plan routes with precision. Consolidate shipments when possible. Avoid sending out half-full trucks. Even shifting delivery days by one can unlock huge savings. If you have only 20-30 ft of trailer space make sure to ask TLI for a partial truckload instead of a dedicated load to save money.
2. Improve Communication Across Teams:
Sales, purchasing, warehouse, and logistics teams should meet regularly. If there are two departments butting heads, it is most likely a communication breakdown rather than a personality conflict. Unsaid expectations are often the largest points of frustration, so ensure your team knows what their deliverables are and then hold each other accountable. When everyone understands what’s coming, they can plan and execute better. No surprises means fewer delays.
3. Audit Frequently:
Don’t wait until something goes wrong. Schedule regular audits of workflows, processes and delegate the auditing of freight invoices, shipment patterns, and carrier compliance. Spot issues before they become expensive problems.
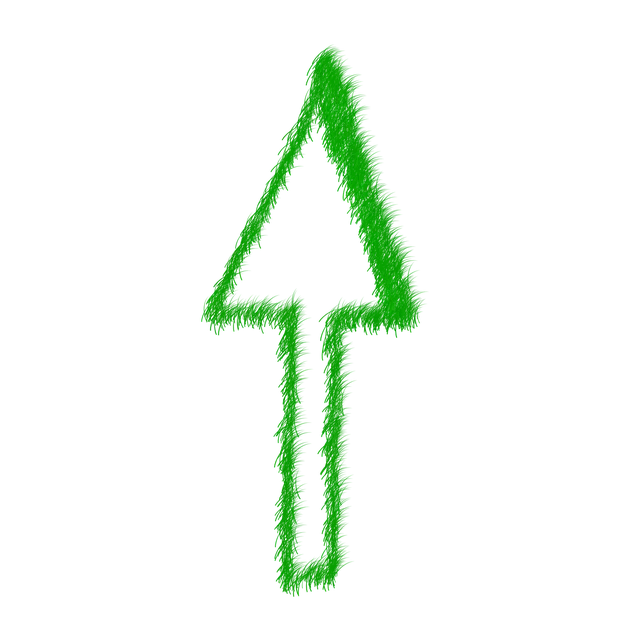